Bulk Site Self Inspection Introduction
TELONE™ customers take pride in their storage facilities. A key part of that vision is doing a periodic, thorough inspections of the facility to catch and correct items BEFORE issues arise. This blog post will take a loot at our Bulk Site Inspection checklist to help avoid blind spots and give guidance on EPA requirements for pesticide storage.
You can download a pdf version of this checklist here.
Let’s dive in.
BULK SITE SELF-INSPECTION
You take pride in maintaining your facility as a safe place to work, reliably storing and transferring product, protecting the environment, and complying with all regulations. A key part of achieving that vision is to periodically look at your facility in a methodical fashion to catch and fix items before they become issues. Nobody knows your facility better than you, but a written self-inspection checklist helps to avoid blind spots.
In 40 CFR 165.90, EPA requires you to inspect each bulk tank, its appurtenances, and each containment structure at least monthly while pesticides are stored or dispensed on the containment structure. Also, 40 CFR 165.95 says you must keep records of these inspections—and specific maintenance performed—for 3 years and be able to furnish those records to the EPA, if requested. Records must include name of the person conducting the inspection or maintenance, date the inspection or maintenance was conducted, conditions noted, and specific maintenance performed.
Below, we list suggested items to include during your bulk site inspections. Customize this list to fit your facility, such as added requirements for rail delivery or site security. The example list focuses on physical items at the bulk site and does not include administrative items like repackaging agreements, or DOT requirements for your vehicles.
Assign the responsibility to the right person in your facility. Make sure there is a system to follow-up on any items found.
Remember, bulk site maintenance may be reimbursable under the Teleos stewardship program. Consult your TELONE™ Sales Specialist and keep a file of receipts.
While there is some overlap, each inspection or assessment fills a separate need. Here we breakdown the difference between various inspection-types:
- SELF-INSPECTIONS: Performed by the facility. Required by EPA.
- AASA INSPECTIONS: American Agronomic Stewardship Alliance. Focused on bulk pesticide facilities. Sponsored and paid for by Ag industry basic manufacturers. Every three years. www.aginspect.com
- RESPONSIBLE-AG ASSESMENTS: Broad-scoped assessment paid for by participating retailer. Covers much wider range of topics than others on this list. Three year cycle. www.responsibleag.org.
- TELEOS INSPECTIONS: Focused on issues specific to TELONE™ soil fumigant products.
BONUS TIP: You can look up the actual regulations affecting your bulk facility by searching online at The Code of Federal Enforcements (https://www.ecfr.gov/). Many key EPA regulations affecting pesticide bulk facilities are mostly found in Title 40 Part 165.
SUGGESTED ITEMS FOR BULK SITE PERIODIC SELF-INSPECTION
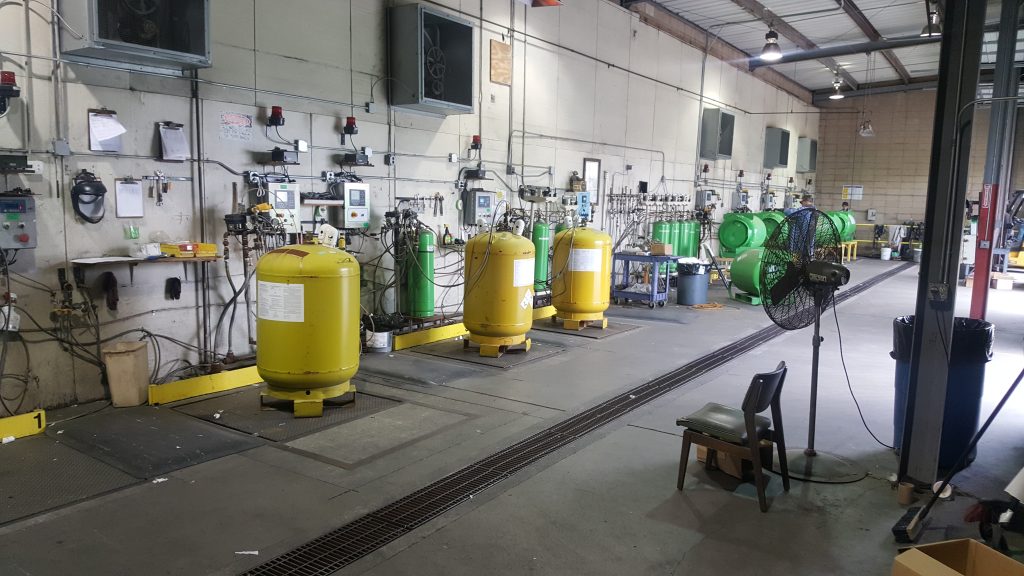
We suggest that you create a form to indicate whether an item is OK, if action is needed, or if the item in question is not applicable. Include person’s name, date, and a space for notes. Make sure follow-ups are completed and documented. Keep records for at least three years. Here are several items we suggest tracking for your bulk-site self inspections:
PRESSURE / VACUUM RELIEF VENTS (PVRVS)
- Disassemble, inspect, and clean PVRVs on both the air drier and tank top. Note: the top of the tank valve has a lighter pressure setting and a heavier vacuum setting. Position air intake opposite of prevailing winds to minimize dirt plugging.
EMERGENCY RELIEF VENT (ERV)
- Check all styles for corrosion, debris, or gasket integrity. Ensure that long-bolt style ERVs move freely and are not corroded. Replace with stainless steel bolts, if necessary. Replace any gasket which is not intact and in good shape.
AIR DRIER OR NITROGEN PAD
- Replace or regenerate desiccant if drier indicator shows it is saturated. Replace desiccant if it shows sign of breakdown. Make sure nitrogen pad valves are open and gauge shows correct pressure on tank. Order new nitrogen if source is low.
FILTERS
- Service regularly. Two types of filters are common: a pressurized screen system and a canister cartridge system. Have new gaskets available; in almost every case the gasket will need to be replaced when the filter is opened for inspection.
FIRE SAFE VALVES
- Replace packing if any sign of leakage is detected.
LABELS AND SIGNAGE
- Inspect and replace any labels or signage, as needed. This includes product label, product booklet, net contents marking, EPA Establishment number marking, NFPA diamond, eye protection required, etc.
EYEWASH, SAFETY SHOWER, FIRE EXTINGUISHERS, PPE
- Test the eyewash and safety shower for proper operation. Ensure that fire extinguishers are up to date on inspections.
HOSES AND DRY DISCONNECTS
- Replace hoses that show damage or deterioration. Check dry disconnects for any deterioration of seals. Repair as necessary. Confirm that dust caps are being used.
ELECTRICAL
- Inspect wiring for deterioration. Look for any electrical components that don’t adhere to Hazard Zone, a.k.a. “explosion proof” standards. For example, do not use a regular extension cord in the Hazard Zone. Only “explosion proof” components are allowed.
GROUNDING AND BONDING
- Inspect the grounding cable that is utilized during loading and off-loading.
DIKE AND LOAD PAD
- Inspect dike walls and floors for cracks. Repair as necessary.
PUMPS, VALVES, PIPING
- Inspect pump and all valves in system. Replace pump seals and any valves if any sign of leakage is detected.
MANHOLE GASKET
- Inspect tank manhole gasket. Replace the gasket if any leakage/weeping is detected around the manhole bolts
TANK
- Seeping at weld seams or corrosion requires further evaluation.
- TIP SHEET: PLACARDING FOR BULK SHIPMENT RETURNS - August 15, 2025
- Stewardship Tip Sheet: Tamper-Evident Packaging Requirements - July 14, 2025
- 2025 PNW Stewardship Meetings - June 11, 2025